Comprehending Porosity in Welding: Checking Out Reasons, Results, and Prevention Strategies
As professionals in the welding industry are well mindful, comprehending the causes, results, and prevention strategies related to porosity is critical for accomplishing robust and trustworthy welds. By diving right into the root creates of porosity, analyzing its destructive impacts on weld quality, and discovering effective prevention strategies, welders can improve their understanding and skills to create high-grade welds consistently.
Typical Reasons For Porosity
Contamination, in the form of dirt, oil, or corrosion on the welding surface area, creates gas pockets when heated, leading to porosity in the weld. Improper shielding happens when the protecting gas, frequently utilized in processes like MIG and TIG welding, is incapable to fully protect the molten weld swimming pool from reacting with the surrounding air, resulting in gas entrapment and succeeding porosity. Furthermore, inadequate gas insurance coverage, usually due to incorrect flow rates or nozzle positioning, can leave components of the weld unsafe, allowing porosity to develop.
Results on Weld Quality
The existence of porosity in a weld can dramatically jeopardize the total quality and integrity of the welded joint. Porosity within a weld creates spaces or tooth cavities that deteriorate the structure, making it extra at risk to fracturing, rust, and mechanical failure.
In addition, porosity can hinder the efficiency of non-destructive screening (NDT) methods, making it challenging to spot various other flaws or stoppages within the weld. This can cause substantial safety and security issues, specifically in crucial applications where the structural integrity of the welded elements is extremely important.
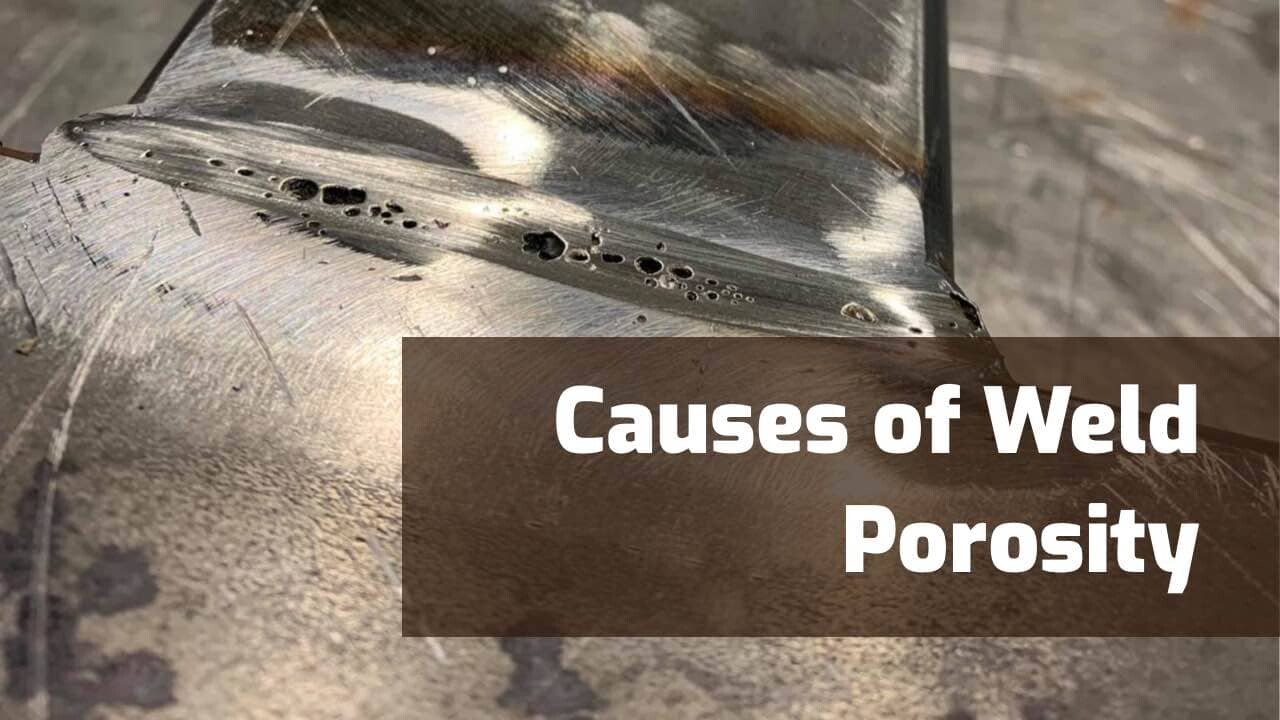
Prevention Techniques Introduction
Offered the harmful influence of porosity on weld high quality, effective avoidance strategies are important to preserving the architectural integrity of welded joints. Furthermore, picking the suitable welding parameters, such as voltage, present, and travel speed, can help minimize the danger of porosity development. By including these avoidance strategies right into welding methods, the occurrence of porosity click site can be significantly decreased, leading to more powerful and a lot more reputable welded joints.
Relevance of Correct Protecting
Proper shielding in welding plays an essential function in avoiding atmospheric contamination and making certain the honesty of welded joints. Protecting gases, such as argon, helium, or try this a mixture of both, are typically used to shield the weld swimming pool from reacting with aspects in the air like oxygen and nitrogen. When these reactive components enter call with the hot weld pool, they can create porosity, bring about weak welds with minimized mechanical homes.

Insufficient shielding can lead to various flaws like porosity, spatter, and oxidation, compromising the architectural stability of the bonded joint. Therefore, adhering to correct shielding techniques is necessary to create high-quality welds with minimal issues and make certain the durability and reliability of the welded elements (What is Porosity).
Tracking and Control Approaches
How can welders effectively keep an eye on and manage the welding procedure to guarantee optimal results and prevent flaws like porosity? By continuously keeping track of these variables, welders can determine variances from the suitable conditions and make instant adjustments to stop porosity development.

Additionally, carrying out correct training programs for welders is essential for keeping an eye on and regulating the welding procedure efficiently. What is Porosity. Educating welders on the importance of maintaining regular criteria, such as appropriate gas protecting and travel speed, can help prevent porosity problems. Normal assessments and qualifications can likewise ensure that welders excel in surveillance and managing welding processes
Additionally, using automated welding systems can boost surveillance and control capabilities. These systems can specifically manage welding parameters, lowering the chance of human error and making sure constant weld quality. By combining sophisticated surveillance technologies, training programs, and automated systems, welders can successfully check and control the welding procedure to decrease porosity defects and achieve high-quality welds.
Verdict
